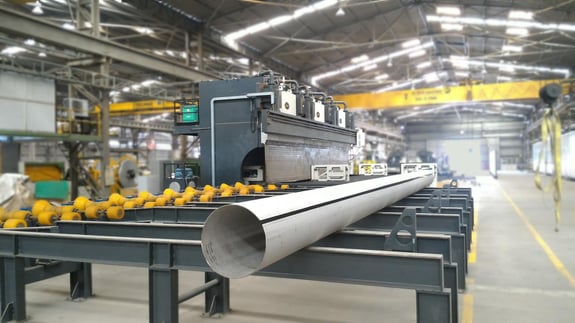
A Complete Guide to Pole Welding: Everything You Need to Know
Setting up a pole welding plant is a strategic investment for industries involved in infrastructure, power distribution, and urban development. From choosing the right welding process to acquiring essential equipment and meeting regulatory requirements, every step plays a crucial role in ensuring efficiency and compliance. This guide will walk you through the key aspects of starting a pole welding plant, helping you make informed decisions for a successful operation.
On this page:
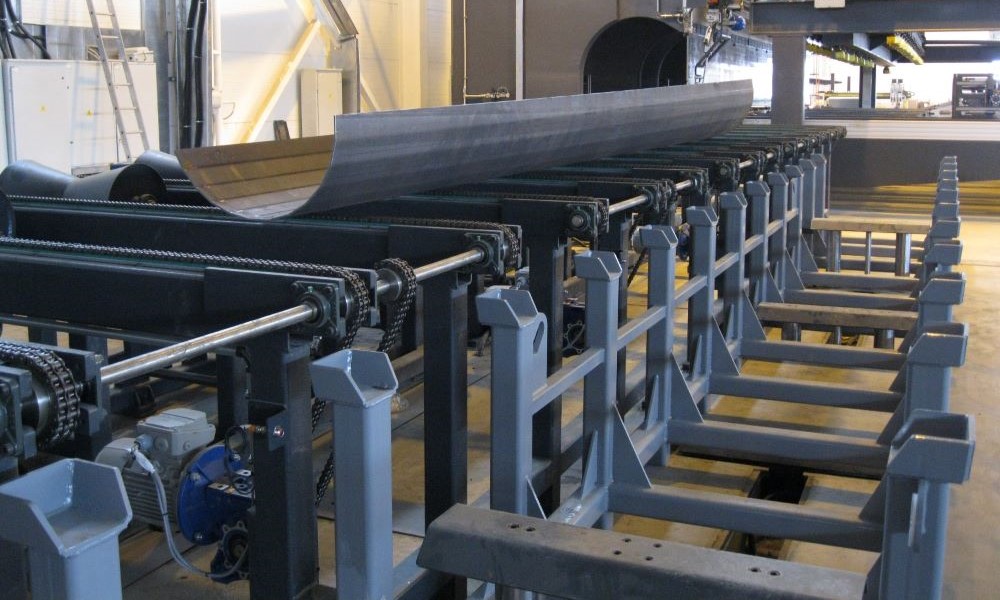
What is Pole Welding? Definition and Applications
Pole welding is a specialized welding process used to fabricate and assemble metal poles for various applications, including construction, electrical infrastructure, street lighting, and telecommunications. The primary goal of pole welding is to ensure strong, durable joints that can withstand environmental stress, corrosion, and heavy loads.
This process is crucial in industries where vertical structures must maintain structural integrity over long periods. Whether used for power transmission lines or urban lighting, properly welded poles play a key role in infrastructure safety and longevity.
Types of Welding Processes Used for Poles
Several welding methods are suitable for pole manufacturing, each with its own advantages:
- Stick Welding (SMAW — Shielded Metal Arc Welding): a versatile and widely used method, ideal for outdoor applications due to its resistance to wind and contaminants.
- MIG Welding (GMAW — Gas Metal Arc Welding): provides high efficiency and cleaner welds, making it suitable for high-volume production. However, it requires a controlled environment.
- Flux-Cored Welding (FCAW — Flux-Cored Arc Welding): similar to MIG welding but with better penetration and higher deposition rates, often used for structural components requiring deep, strong welds.
Choosing the right welding method depends on factors such as material thickness, production volume, and environmental conditions at the manufacturing site.
Key Equipment and Materials for Pole Welding Plants
Setting up a pole welding plant requires investing in high-quality machinery and materials. The most important equipment includes:
- Pole Welding Machines: these machines ensure precision, efficiency, and uniform welds for high-volume production.
- Multi-press brakes: Bending plant consisting of multiple in-line press brakes for the production of round tapered poles and polygonal poles and towers. The system automatically produces up to lengths of 16 meters and weights up to 15 tons.
- Roto Systems: used for the production of aluminum lighting poles and flagpoles.

How to Start a Pole Welding Plant: Administrative and Bureaucratic Procedures
Starting a pole welding plant requires navigating several legal and regulatory requirements. Here’s an overview of the key steps:
- Business registration and licensing: obtain the necessary permits and licenses from local and national authorities.
- Environmental and safety compliance: ensure that your plant meets workplace safety standards and environmental regulations, including waste disposal and emissions control.
- Workforce certification: welders and operators should be certified according to industry standards.
- Facility setup and quality control: invest in quality control processes to meet customer and regulatory requirements.
SOMO can help you in every step of opening a new pole production plant.
Contact us for more informationSafety Precautions and Challenges in Pole Welding
Welding metal poles presents specific safety challenges and requires strict adherence to safety protocols.
Key precautions include:
- Proper ventilation and fume extraction: prevents exposure to harmful welding fumes.
- Personal Protective Equipment (PPE): includes welding helmets, gloves, fire-resistant clothing, and respiratory protection.
- Fire prevention measures: fire-resistant barriers and emergency plans should be in place.
Common Welding Challenges
Some of the most common welding issues include:
- Porosity: caused by contamination or improper shielding gas coverage.
- Distortion and warping: results from excessive heat input, requiring proper heat control.
- Cracking: often due to poor material selection or inadequate preheating.
- Lack of fusion: happens when weld beads do not properly penetrate the metal surface, weakening the structure.
Implementing best practices in quality control and using advanced welding techniques can help minimize these challenges and improve overall production efficiency.
We can help you to develop a full equipment compliance and productive pole welding plant
Contact us for more informationReferences
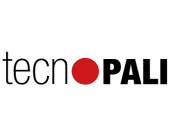
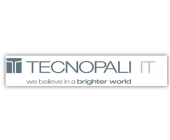

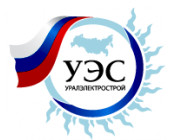
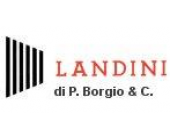
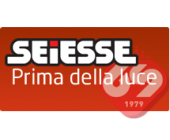
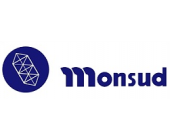
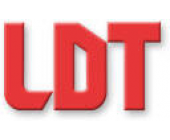
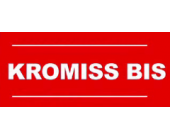
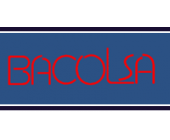
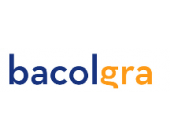
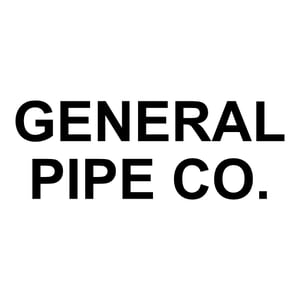
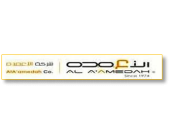
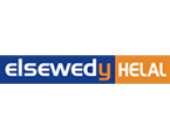
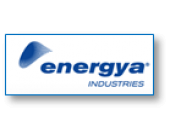
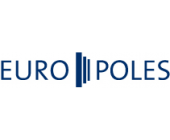
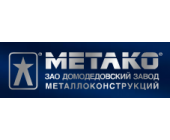
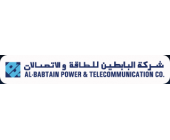
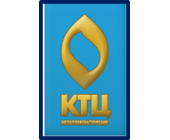

Contact us
Fill the form to receive more information