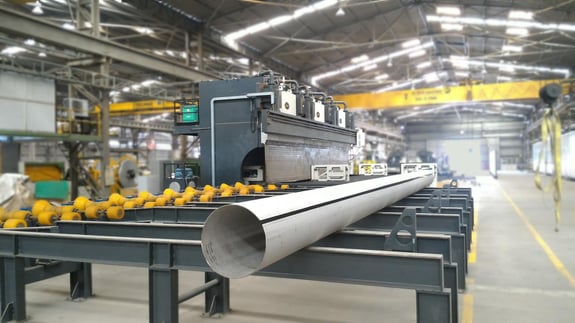
Press Brake Manufacturing
Press brakes are essential for manufacturing large pipes and poles. On this page, we explore how the bending process works and the role SOMO’s advanced systems play in precision-driven metal forming.
Table of Contents:
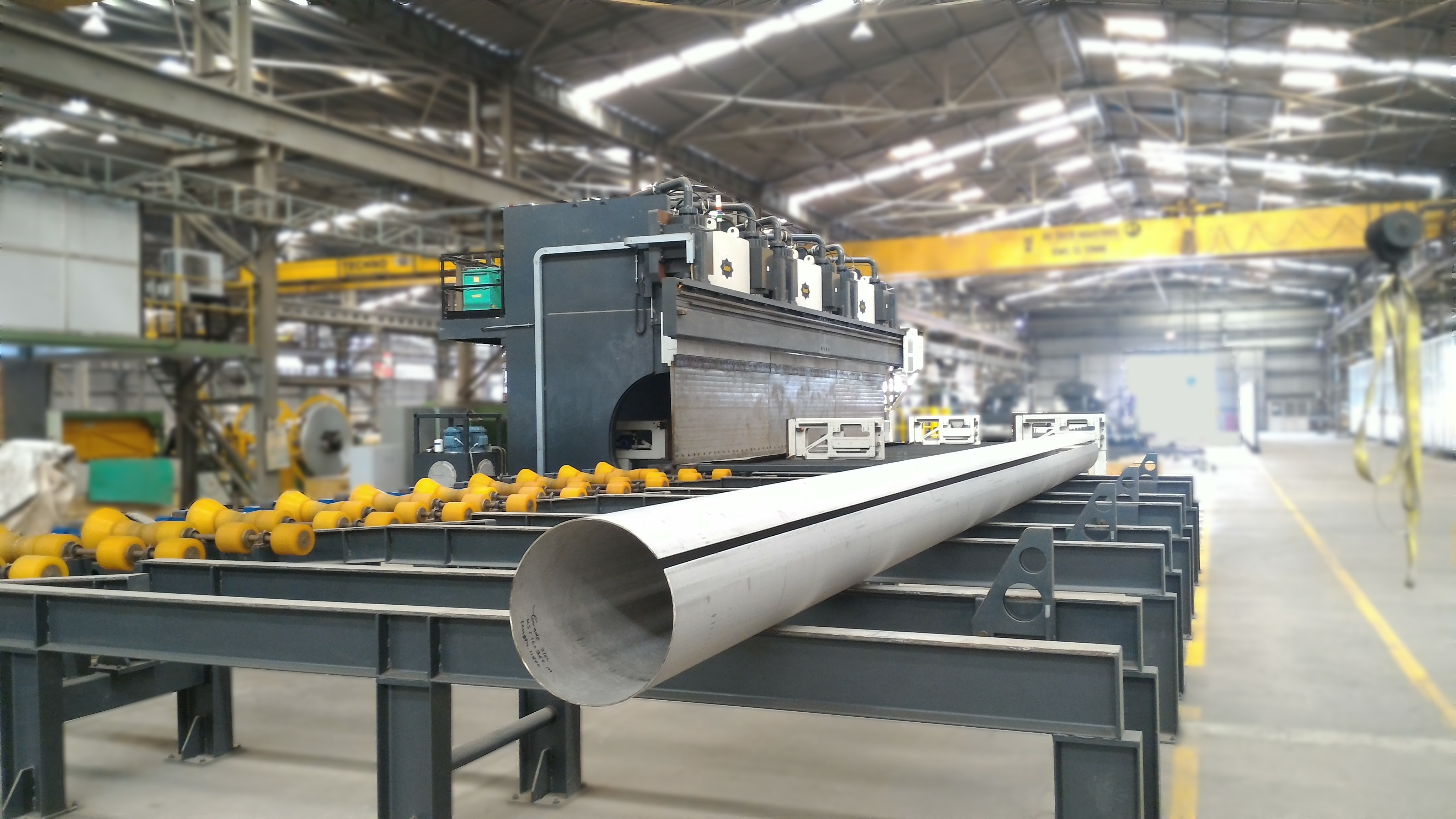
What does a press brake do?
A press brake is a powerful industrial machine used to bend metal sheets with high precision. In the specific case of SOMO’s production, press brakes are designed for the manufacturing of pipes and poles, particularly those requiring large diameters, thick materials, and heavy-duty performance.
Unlike standard sheet metal forming, pipe and pole manufacturing involves synchronised, large-scale bending operations. SOMO press brakes are capable of processing sheets up to 16 metres in length and 15 tons in weight, ensuring durability and exact specifications across every workpiece.
These machines are vital for:
- Creating consistent geometries in cylindrical and conical pipe segments
- Forming polygonal and tapered poles with exact angles
- Supporting further welding and assembly processes with precision-bent metal components
How does the bending process work?
The bending process within SOMO’s manufacturing lines is fully CNC-controlled and automated, ensuring repeatability and speed. Here’s how it works:
- Sheet positioning: large metal plates are placed into the machine.
- Synchronised control: multiple press brakes operate in sequence or in parallel.
- Bending operation: using high-tonnage force, the punch presses the sheet into the die, forming the desired angle or shape.
- Automated output: the system completes the part and prepares for the next operation (welding, forming, etc.).
Thanks to numerical control, all parameters such as bending angle, pressure, and sheet alignment are precisely programmed. This is especially important in JCO bending systems (used for pipes), where accuracy is key to producing sections that will be later welded into large-diameter tubes.
What is JCO bending technique and why is it convenient?
The JCO bending technique is particularly used in the production of pipes for the Oil & Gas sector due to its flexibility and precision. The process consists of three main phases:
- Phase J: the sheet metal is partially bent on one side, forming a "J" shape.
- Phase C: next, it is bent along the other side, taking on a "C" shape, with the edges starting to align.
- Phase O: finally, a complete cylinder in the shape of an "O" is obtained, ready for welding.
Advantages of JCO bending:
- Flexibility: Production of pipes with various diameters.
- Precision: Optimal edge alignment for perfect welding.
- Suitable for pipes with a diameter/thickness ratio of up to 9:1.
SOMO designs and produces cutting-edge press brakes for pipe and pole manufacturing, with a wide range of configurations to match any industrial requirement.
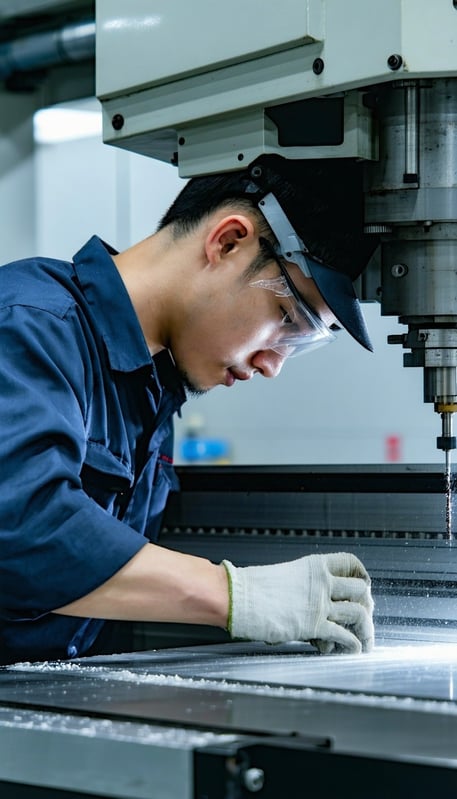
Looking for a solution tailored to your production line?
Contact our team now to learn more about our technology and receive expert advice.What does a press brake cost?
The cost of a press brake varies based on several factors:
- Bending capacity (tonnage)
- Level of automation (manual vs. CNC)
- Number of press units in the line
- Custom features for pipe or pole production
At SOMO, we offer flexible, scalable solutions to suit different budget levels. From compact CNC press brakes to multi-unit automated bending plants, we help businesses optimise cost-efficiency and production speed.
For accurate pricing and configuration support, contact us directly — our team is ready to help.
Types of press brakes manufactured by SOMO Produzione
SOMO Produzione specialises in industrial press brake manufacturing for large-scale pipe and pole production. Our technology focuses exclusively on heavy-duty applications where precision and synchronisation are critical.
Press brake for pipe manufacturing
Our pipe production systems consist of:
- Two or more synchronised CNC press brakes
- Full support for JCO bending processes
- Automated handling and output for large-diameter, thick-wall pipes
These systems are ideal for industries such as oil & gas, infrastructure, and shipbuilding.
Key benefits:
- High-speed operation
- Consistent pipe roundness and weld-readiness
- Reduced material waste
Press brake for pole manufacturing
SOMO also builds high-performance lines for producing:
- Round tapered poles
- Polygonal poles and towers
These systems are built using synchronised CNC press brakes arranged in-line, allowing them to:
- Handle parts up to 16 metres long
- Support metal sheets weighing up to 15 tonnes
- Achieve complex geometries with full automation
This technology is commonly used for light poles, telecommunication towers, and urban infrastructure elements.
Key benefits:
- Precise tapering and polygonal shapes
- Modular system design
- Long-term production stability
Innovative ideas drive industrial success
At SOMO, we believe that innovation in press brake technology is a key driver for industrial competitiveness. Our solutions:
- Reduce labour input through automation
- Enhance energy efficiency and resource use
- Ensure the highest standards of bending precision
By choosing SOMO, you're investing in technology that supports long-term growth and operational excellence in pipe and pole manufacturing.
Ready to upgrade your bending capabilities?
Get in touch today to request more information or a customised quote.References
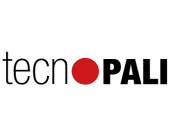
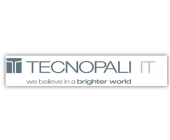

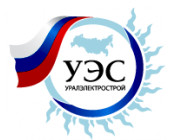
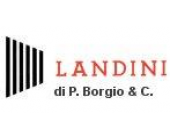
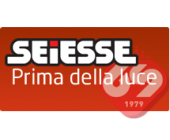
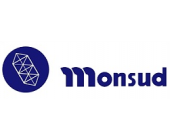
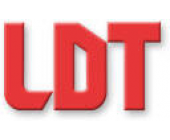
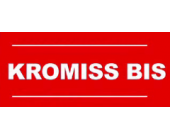
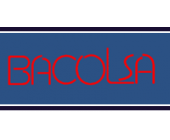
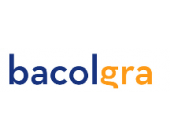
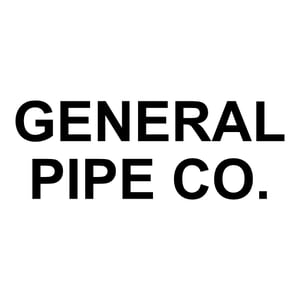
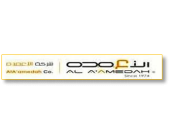
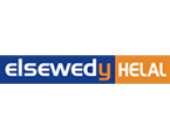
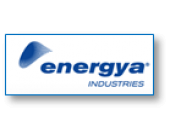
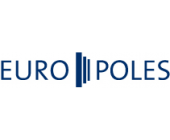
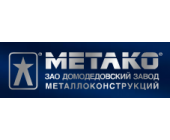
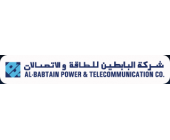
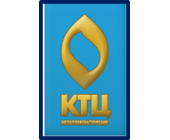

Contact us
Fill the form to receive more information