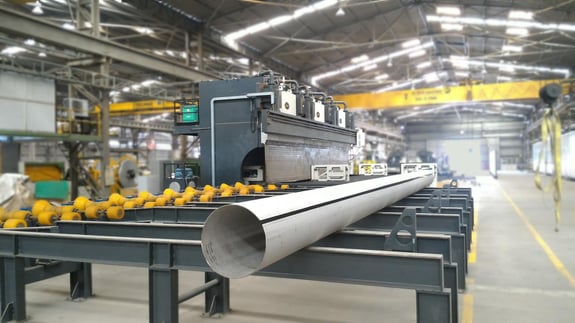
Tack Welding Pipe: Essential Guide for Efficient Pipe Manufacturing
Tack welding is a fundamental process in pipe manufacturing, ensuring proper alignment and structural integrity before final welding. This technique is widely used in welded pipe for industries such as oil & gas, water infrastructure, and structural steel, where precision and durability are essential. On this page, we explore the importance of tack welding, its role in pipe fabrication, and how SOMO Produzione’s advanced machinery enhances the process.
Table of Contents:
Plants for pipe production
Longitudinally welded pipe (LSAW) plants, suitable for a wide range of applications.
Special applications
Plants made according to specific customer's requirements, equipped with customized equipment and devices.
What is Tack Welding in Pipe Manufacturing?
Tack welding is a type of resistance welding that joins two or more metal pieces using heat generated by electrical resistance. This method stands out for its precision and its ability to create localized joints without significantly altering the properties of the surrounding materials.
It is widely used in the pipe manufacturing for different sectors and in the automotive, aerospace, and other industries.
How Does Tack Welding Work?
The working principle is surprisingly simple yet incredibly effective.
Two copper electrodes, powered by an electric current, press the metal surfaces together. The current flow generates localized heat, which melts the metal at the contact point, creating a strong and precise weld.
The temperature at the contact point can exceed 1500°C, but the heat remains concentrated exactly where it is needed. This ensures clean welds without deforming the surrounding areas of the material.
Tack Welding Procedure in Pipe Production
Achieving high-quality tack welds requires a precise and methodical approach. Every stage of the process plays a crucial role in the final outcome, and skipping even a single step could compromise the strength and durability of the joint.
Let’s go through the process step by step.
The procedure consists of four key stages:
- Preparation – Thoroughly clean the surfaces to be welded and ensure the materials are compatible. Remove any traces of oxide, paint, oil, or contaminants that could interfere with the welding process.
- Positioning – Align the metal pieces correctly between the electrodes. Make sure the surfaces are in full contact and that the electrodes are precisely positioned at the intended welding points.
- Welding – Apply pressure and electrical current for the required duration. The pressure must remain consistent, and the current should be adjusted based on the material type and thickness.
- Cooling – Allow the weld to cool completely before handling the workpiece. This step is essential to ensure proper crystallization of the metal, which directly affects the weld’s strength.
Technical Welding Parameters
Setting the correct technical parameters is essential for achieving high-quality welds. Each material and thickness requires a specific combination of values to ensure optimal results.
For Mild Steel:
- Temperature: 1200-1500°C
- Welding Time: 10-50 milliseconds
- Pressure: 2-5 bar for thin sheets
- Current: 4000-8000 amperes, depending on thickness
For Stainless Steel:
- Temperature: 1350-1600°C
- Welding Time: 15-60 milliseconds
- Pressure: 3-6 bar
- Current: 5000-9000 amperes
For Aluminium:
- Temperature: 600-650°C
- Welding Time: 5-20 milliseconds
- Pressure: 1.5-4 bar
- Current: 15000-25000 amperes
Material thickness has a significant impact on these parameters. For every additional millimetre of thickness, the welding current should be increased by approximately 1000 amperes, and the welding time should be extended by 10 milliseconds.
SOMO’s Machinery for Tack Welding Pipe
SOMO Produzione specializes in high-performance pipe manufacturing solutions, including state-of-the-art tack welding systems designed for precision, efficiency, and durability.
Overview of SOMO’s Pipe Production Solutions:
- Advanced automation for consistent and high-speed welding.
- Customizable systems for various pipe sizes and materials.
- Integrated quality control for superior weld consistency.
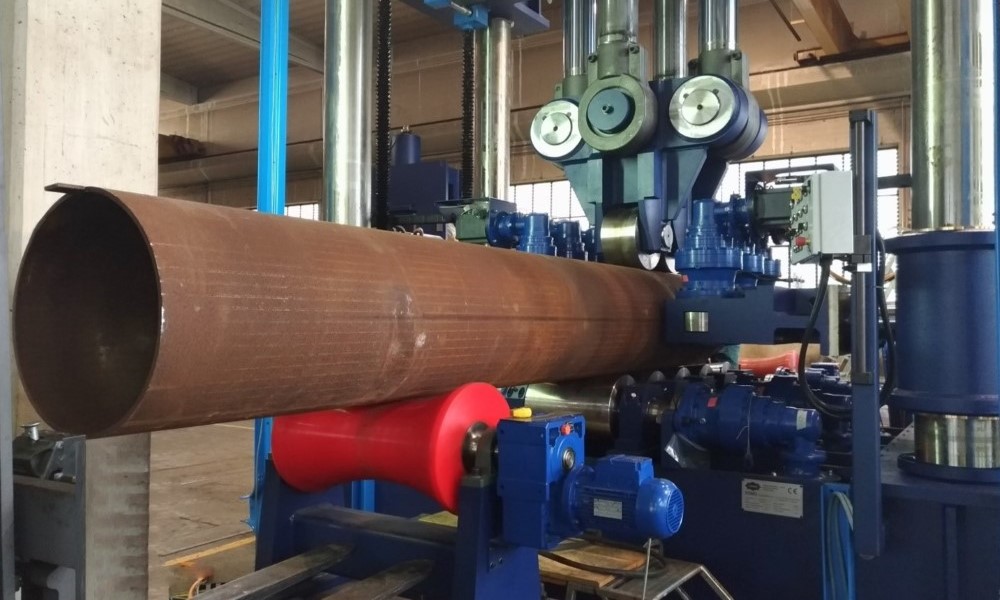
Applications of Tack Welding in Pipe Industries
Tack welding is essential in multiple industrial sectors, ensuring strong and precise welds in critical infrastructure projects.
Oil & Gas Pipelines:
- Ensures leak-proof joints for high-pressure gas and oil transportation.
- Supports large-diameter pipe welding, preventing alignment issues.
- Reduces risks of defects that could lead to pipeline failures.
Water and Sewage Systems:
- Provides durable, corrosion-resistant welds for water supply networks.
- Ensures tight sealing, preventing leaks and contamination.
- Supports the production of high-capacity pipes for urban infrastructure.
Structural Steel and Industrial Piping:
- Used in construction and heavy industries for robust piping systems.
- Improves structural integrity in factories, refineries, and power plants.
- Allows for precise welding in high-stress applications.
Tack welding is a vital step in pipe manufacturing, ensuring high-quality, durable, and precise welds for industrial applications. SOMO Produzione’s innovative welding machinery optimizes the process, delivering efficiency, accuracy, and long-lasting results. Investing in state-of-the-art tack welding technology is key to achieving superior pipe production standards in today's competitive market.
For more information about SOMO Produzione’s tack welding solutions
Upgrade your steel pipe plant with SOMO’s industry-leading solutions.References
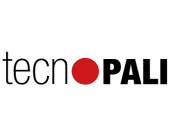
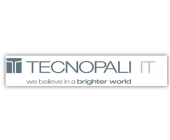

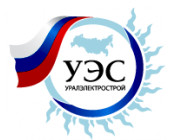
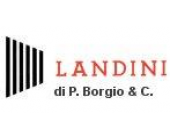
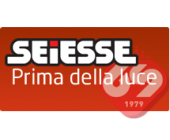
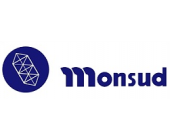
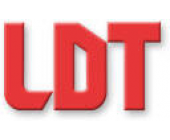
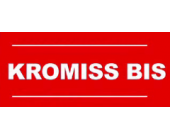
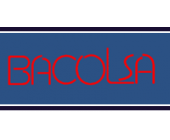
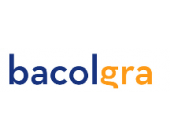
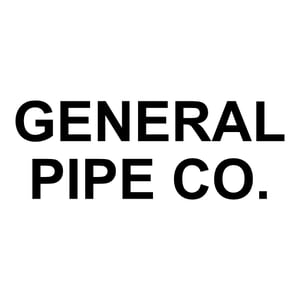
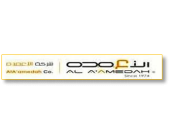
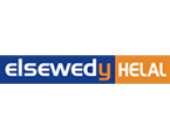
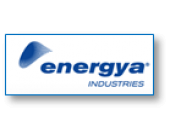
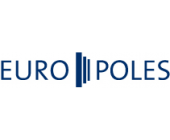
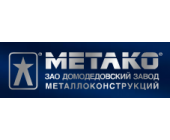
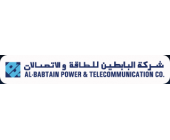
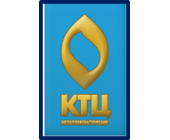

Contact us
Fill the form to receive more information